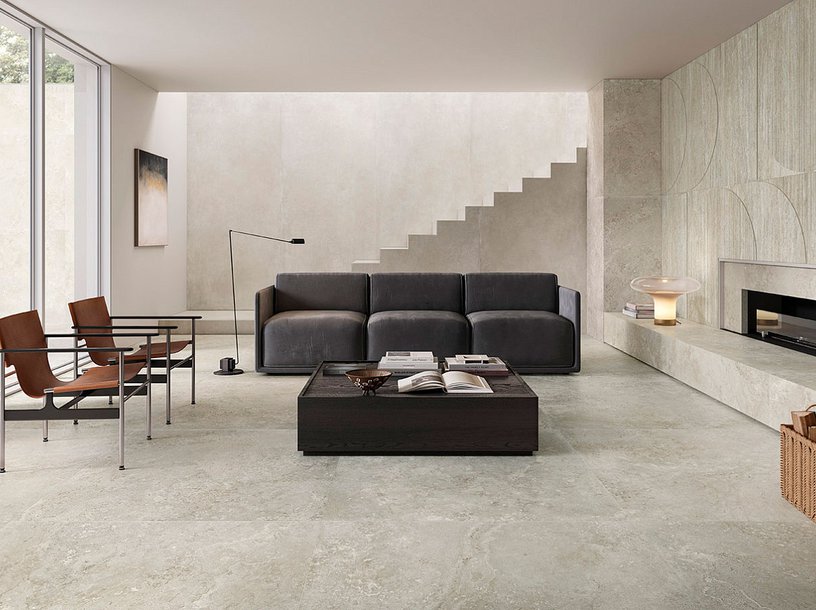
Керамогранит изготавливают из натурального сырья, которое не выделяет токсичных газов и не содержит летучих органических соединений. Этот материал обладает высокой гигиеничностью, так как его низкая пористость не позволяет жидкостям впитываться и задерживать бактерии, запахи и грязь. Керамогранит гипоаллергенен, экологичен и подходит для вторичной переработки.
Его производят из натуральных глиняных смесей, которые готовят в длинных печах при температуре до 1200 °C. Благодаря этим температурам плитка и крупные плиты из керамогранита приобретают невероятную механическую прочность, пожаробезопасность и морозостойкость.
Дизайн керамогранита
Дизайн продукта — это сложная деятельность, включающая в себя различные виды работы отдела маркетинга и тесно связанная со стратегией компании. Она включает в себя:
- изучение потребностей клиентов;
- изучение бестселлеров конкурентов;
- определение проекта;
- эстетическую доработку коллекции;
- создание прототипов;
- индустриализацию.
Дизайн продукта связан с подготовкой коммерческого запуска, так как они идут рука об руку. Решение этой проблемы, когда коллекция уже находится в производстве, может сильно задержать время прибытия в выставочный зал, что приведёт к слишком большой дистанции между запросом рынка и реакцией производителя.
Цикл производства керамогранита начинается со склада сырья. Ингредиенты рецепта керамогранита включают глины, каолины, полевые шпаты, пески и другие минералы различного цвета и зернистости. Глина и каолин придают смеси связующие свойства и пластичность, а также позволяют плитке сохранять форму после прессования. Каолин — ценный вид глины, который может гарантировать высокую степень белизны смеси. Его можно использовать для получения матового эффекта.
Состав керамогранита
Производство керамогранита начинается со склада сырья, поэтому важно понимать, какие ингредиенты используются в процессе.
В состав керамогранита входят натуральные компоненты, которые были отобраны с учётом их химико-физических характеристик и чистоты. К таким компонентам относятся глины, каолины, полевые шпаты, пески и другие минералы разного цвета и зернистости. Глины и каолины придают смеси связующие свойства и пластичность, а также позволяют плитке сохранять форму после прессования. Каолин — это ценный вид глины, который может обеспечить высокую степень белизны смеси. Его можно использовать для создания матового эффекта, в зависимости от запросов рынка.
Полевые шпаты являются наиболее распространённой группой минералов на Земле и присутствуют во всех типах горных пород. Они придают твёрдость и прочность другим материалам, делая их более устойчивыми к ударам. Кроме того, полевые шпаты играют важную роль в качестве «флюсов», снижая температуру плавления в процессе производства. Песок является основным элементом плитки. Он уменьшает пористость изделий после обжига, облегчая процесс спекания и придавая материалу стойкость, компактность и долговечность. Цвет плитки достигается за счёт добавления оксидов металлов.
Этапы производства керамогранитной плитки
Процесс производства керамогранита можно разделить на несколько основных этапов:
- Подготовка сырья. На этом этапе происходит качественный анализ и измельчение ингредиентов. Затем добавляют большое количество воды, чтобы получить жидкий раствор, называемый «шликером».
- Распыление. Это химико-физический процесс, который приводит к отделению порошков от водной части. Порошки становятся очень мелкими, а водная часть испаряется благодаря высоким температурам внутри камеры распыления.
- Уплотнение. Распылённое сырьё прессуют внутри форм. Сила, с которой прижимается смесь, очень велика, что существенно влияет на стойкость керамогранита.
- Сушка. Небольшая влажность, оставшаяся после распыления, дополнительно снижается, если необработанные плитки остаются внутри туннелей с горячим воздухом.
- Приготовление глазури и декорирование. Поверхность необработанной плитки декорируется с помощью цифровых технологий. На этом этапе изделие приобретает свои основные эстетические характеристики.
- Выпекание. Декорированные плитки медленно продвигаются внутри длинных печей, температура которых достигает 1200 °C. Важно постепенно приближать плитки к температуре плавления и столь же постепенно давать им остыть перед тем, как покинуть печь.
- Выбор. Материал проверяется операторами и машинами, оснащёнными роботизированными системами технического зрения, с целью отбраковки несоответствующей плитки.
- Дополнительная обработка. После обжига плитка подвергается шлифовке кромок и притирке поверхности.
- Упаковка. Плитка упаковывается и размещается на поддонах. Большие слябы хранятся в ожидании комплектации.
Как производится тонкий керамогранит
Производство тонкого керамогранита отличается от обычного процесса изготовления керамогранита в некоторых аспектах. Возникает вопрос: делает ли это большие листы уменьшенной толщины другим типом материала? Ответ отрицательный: химико-физический процесс, определяющий структуру материала, то есть спекание, является общим для обоих типов керамических изделий.
Однако при производстве больших листов тонкого керамогранита есть отличие: сырьё не уплотняется внутри форм с помощью буфера, а дозируется на конвейерной ленте и прессуется. Это позволяет достичь впечатляющих форматов, характерных для данной технологии, и избежать внутреннего напряжения материала, которое может возникнуть из-за ограничений традиционной формы.